So! - first off, it's not a kit
I've wanted to work with Ivory for a long, long time. Ultimately, I figured that if I didn't just do it that it would never happen. Bucket list.
So here it is. The trade term is Fossilized Walrus Tusk Ivory. It's not really fossilized...more like 'mineralized' as the tusk sits in the ground for only about 5K - 10K years (like Morta...more on that later)...so the Ivory is not replaced by minerals as in fossilization, the Ivory is colored by the minerals in which it is buried.
Anyway...extreme caution is needed when working it. NO power tools were used in making the knife. Even though this piece was very solid and had excellent integrity, heat is it's enemy and will cause the Ivory to "cloud". Not desirable.
Other than that, the tusk was sized using a fine blade jeweler's saw, then sanded starting with 150 grit...and down through the sizes ending up with a Fabuluster Polishing Cloth. The cloth is impregnated with Rouge on one side and is like chamois on the other. Than, plus 0000 Steel Wool are what gave the Ivory it's final shine. That and some serious elbow grease.
The blade is from Finland. They're the only ones that do this stuff. It's about 2 1/4" long...1 1/2% - 2% Carbon...Rockwell about 65. It is a flat Scandi grind and has to be sharpened using Ceramic or Diamond. It is literally razor sharp with no secondary bevel. I plan to add that to make it more durable as any steel that hard is fragile.
The bolster and metal spacers are pure copper, cut from bar and sheet stock. The three wood spacers are Morta. I thought it would be fun to make a knife where all the organic materials were OLD! The entire fore end is 'sculpted' so that when the knife is taken in hand one's fingers (if right handed) fall into planes that allow for more effective control of the blade. The butt of the handle is diagonal to the length of the tusk and adds to the arc already present in the handle...which is very slightly curved, fitting very well into the palm.
All in all, I'm fairly pleased, especially as it was all done with hand tools.
OK - so now for the pics. It's kinda photo heavy, but seeing at what's 'in' the ivory as one rotates it is what it's all about, at least for me. So I posted more shots than I normally would so some of that would show up.
I've wanted to work with Ivory for a long, long time. Ultimately, I figured that if I didn't just do it that it would never happen. Bucket list.
So here it is. The trade term is Fossilized Walrus Tusk Ivory. It's not really fossilized...more like 'mineralized' as the tusk sits in the ground for only about 5K - 10K years (like Morta...more on that later)...so the Ivory is not replaced by minerals as in fossilization, the Ivory is colored by the minerals in which it is buried.
Anyway...extreme caution is needed when working it. NO power tools were used in making the knife. Even though this piece was very solid and had excellent integrity, heat is it's enemy and will cause the Ivory to "cloud". Not desirable.
Other than that, the tusk was sized using a fine blade jeweler's saw, then sanded starting with 150 grit...and down through the sizes ending up with a Fabuluster Polishing Cloth. The cloth is impregnated with Rouge on one side and is like chamois on the other. Than, plus 0000 Steel Wool are what gave the Ivory it's final shine. That and some serious elbow grease.
The blade is from Finland. They're the only ones that do this stuff. It's about 2 1/4" long...1 1/2% - 2% Carbon...Rockwell about 65. It is a flat Scandi grind and has to be sharpened using Ceramic or Diamond. It is literally razor sharp with no secondary bevel. I plan to add that to make it more durable as any steel that hard is fragile.
The bolster and metal spacers are pure copper, cut from bar and sheet stock. The three wood spacers are Morta. I thought it would be fun to make a knife where all the organic materials were OLD! The entire fore end is 'sculpted' so that when the knife is taken in hand one's fingers (if right handed) fall into planes that allow for more effective control of the blade. The butt of the handle is diagonal to the length of the tusk and adds to the arc already present in the handle...which is very slightly curved, fitting very well into the palm.
All in all, I'm fairly pleased, especially as it was all done with hand tools.
OK - so now for the pics. It's kinda photo heavy, but seeing at what's 'in' the ivory as one rotates it is what it's all about, at least for me. So I posted more shots than I normally would so some of that would show up.
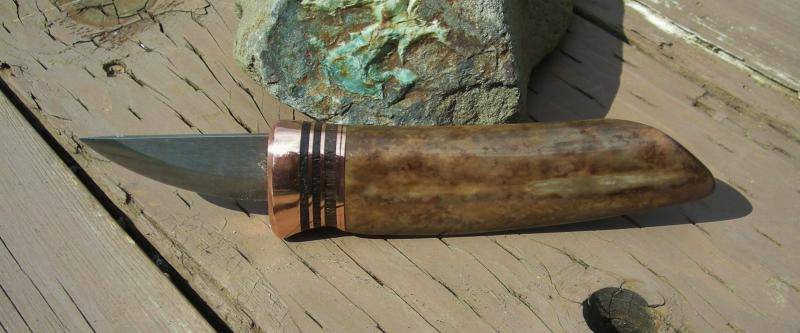
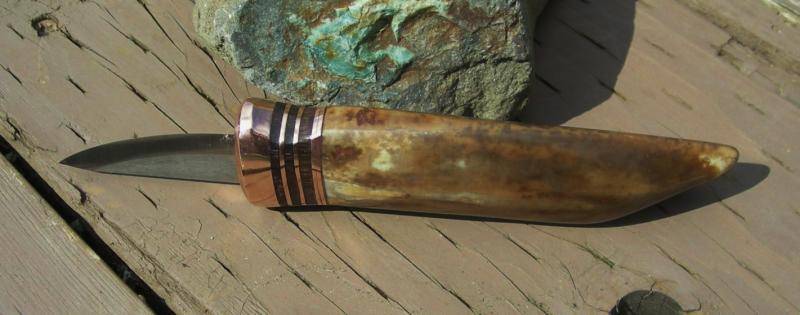
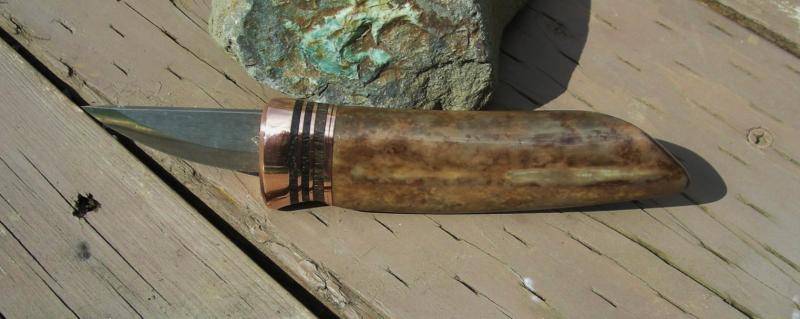
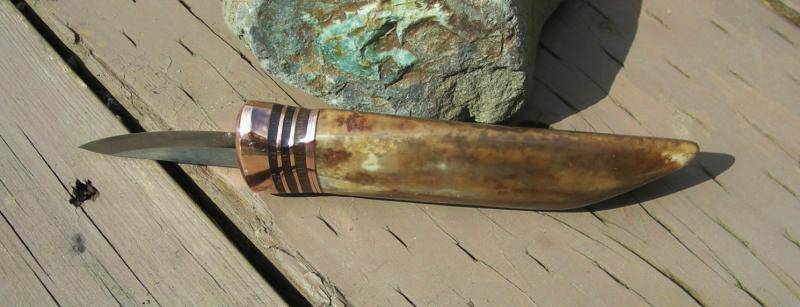
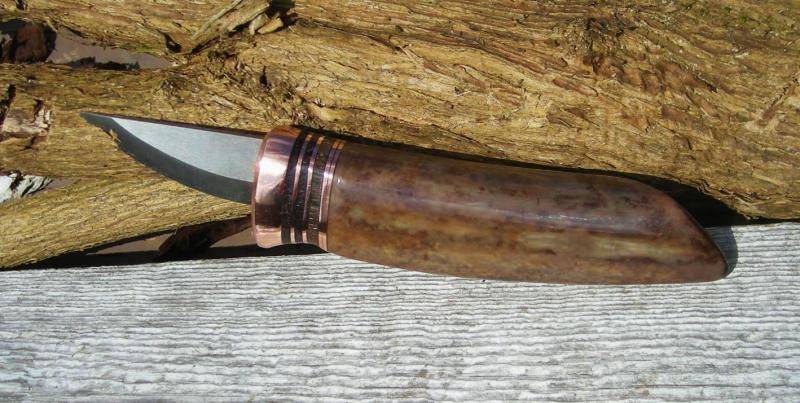
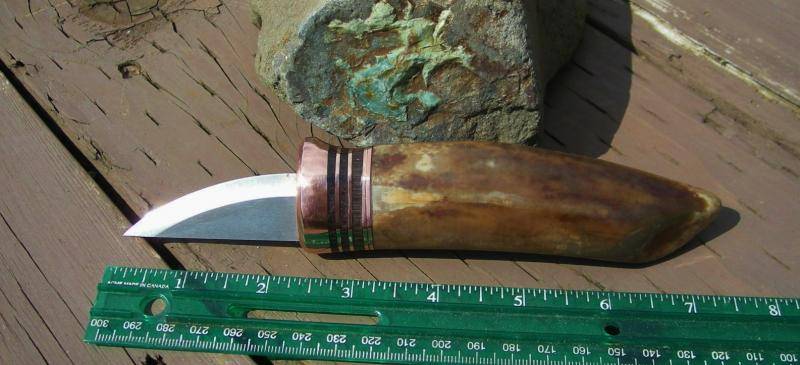