Hawker
Well-known member
- Joined
- May 15, 2012
- Messages
- 743
- Reaction score
- 0
I just finished a couple of three finger drop point knives that are small enough to carry everyday.
They are made from 1 1/2 " X 1/8" ATS-34 Bar Stock. Heat trated to Rockwell hardness of 60.
Overall length is 6" with a 2 5/8" blade.
Once I've ground the blades I hand sand them with 150 grit to 2000 grit wet/dry automotive sand paper folded over a kitchen butter knife to a mirror finish which takes about 4 hrs per side.
When I got the blades back from being cryogenically heat treated in Paul Bos's facility in Idaho they were fitted with dovetail bolsters I made from 1 1/2" X 1/4" brass bar stock that lock the front of the handle material in place when ground to the same angle.
Wenge wood and moose front leg bone was the handle material choosen for these two. This was my first attempt using bone for the handle material and much prefer to work with wood. Especially when fitting the dovetails it's alot easier with squared up material rather than working with curved and rounded edges.
They are made from 1 1/2 " X 1/8" ATS-34 Bar Stock. Heat trated to Rockwell hardness of 60.
Overall length is 6" with a 2 5/8" blade.
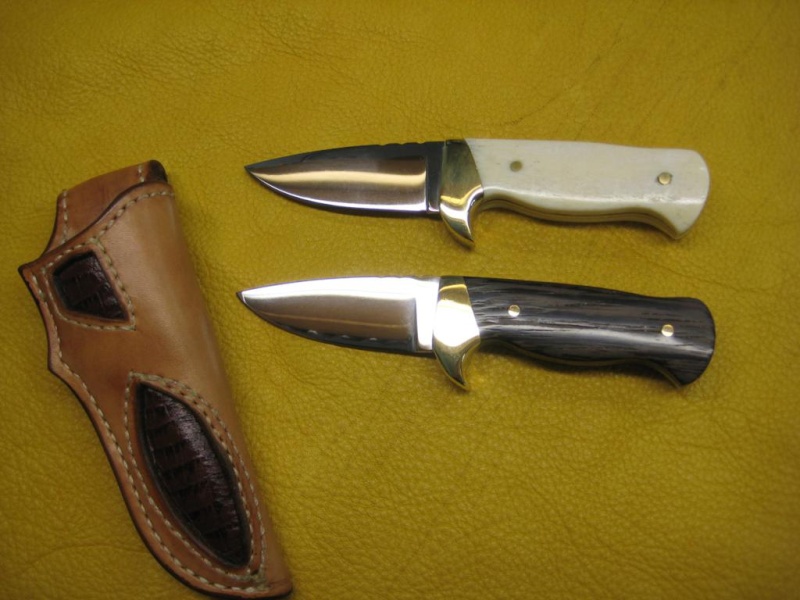
Once I've ground the blades I hand sand them with 150 grit to 2000 grit wet/dry automotive sand paper folded over a kitchen butter knife to a mirror finish which takes about 4 hrs per side.
When I got the blades back from being cryogenically heat treated in Paul Bos's facility in Idaho they were fitted with dovetail bolsters I made from 1 1/2" X 1/4" brass bar stock that lock the front of the handle material in place when ground to the same angle.
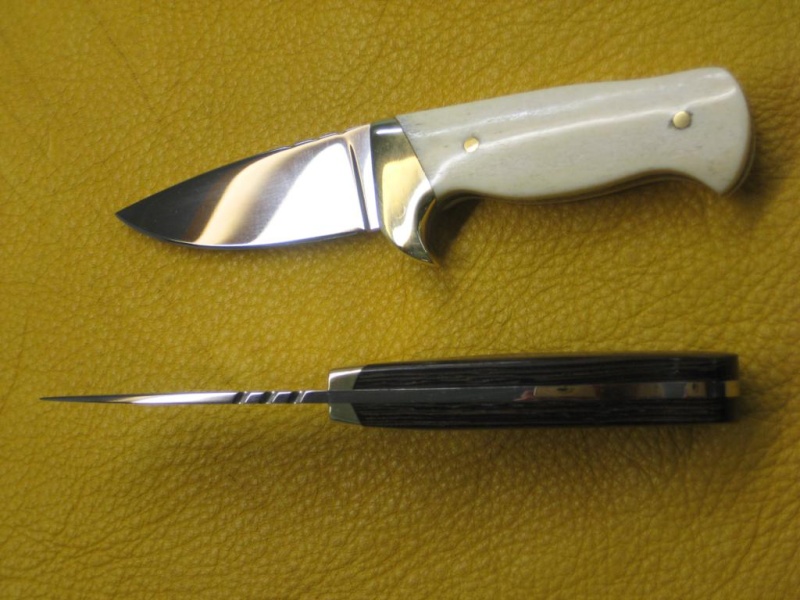
Wenge wood and moose front leg bone was the handle material choosen for these two. This was my first attempt using bone for the handle material and much prefer to work with wood. Especially when fitting the dovetails it's alot easier with squared up material rather than working with curved and rounded edges.
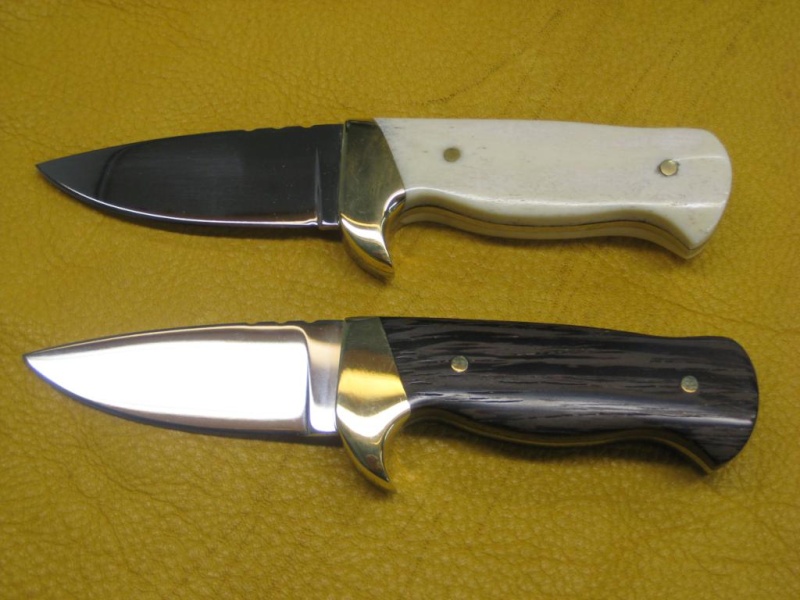